Model | BPS-45T System |
Overall dimensions | L 3,800 x D 1,1,45 x H 3,000 |
Electricity supply | 3 phase electricity 380V |
Hydraulic motor | 3.75 kw |
Chip wheel diameter | Ø 75mm |
Time to press one wheel of chips | 28 second |
Processing capacity | 50~120 kg/h |
Pressing ratio | 20:01 |
Metal Chip Pressing System BPS – 45T
The BPS-45T metal chip compaction system is not just a convenient machining tool but also an efficient and flexible solution for metal manufacturers. Designed with advanced technology and intelligent features, this product offers convenience, quality, and high efficiency for the manufacturing process.
Our compaction system is designed to be flexible and versatile to accommodate all types of metal cutting chips, from wire-like chips to fragmented chips, meeting the diverse needs of the metal processing industries.
The flexibility of our system allows us to handle various types of chips from cutting machines, milling machines, lathes, drilling machines, tapping machines, and many other metal processing equipment.
Whether it’s large or small, thick or thin chips, our compaction system is adjustable to ensure the compaction process is carried out with precision and efficiency. This enhances flexibility, speed, and ensures high quality in the production process, thereby increasing productivity and efficiency of metal production lines.
Our metal chip compactor system is not only designed to ensure optimized operational efficiency but also provides convenience in maintenance and repair. Integrated with an intelligent control system using PLC and HMI, users can easily adjust the parameters and compaction size according to the specific needs of the product.
Furthermore, the compaction system is equipped with powerful hydraulic devices, maximizing the density of metal chips. This not only enhances the quality of the final product but also minimizes the volume of the cut chips to the greatest extent, resulting in material savings and increased production efficiency. Additionally, the stability and reliability of the compaction system ensure that the production process runs continuously and effectively.
- The machine is designed in an industrial style, with a sturdy metal frame, including main components such as the crushing unit, conveyor belt, and compaction unit cleverly arranged side by side. The lid of the crushing unit is rectangular in shape, with a flat design, facilitating the processing operation.
- The body of the machine is funnel-shaped, directly connected to the conveyor belt, which leads to the compaction unit in a rectangular shape, optimizing the working process. On top, beside the compaction unit, is the control panel, arranged systematically, including a control panel and indicator lights, facilitating users to monitor and adjust operations.
- The rear of the machine features an electrical box placed next to the control panel, creating a harmonious and convenient overall design for operation.
Recovering Cutting Oil Residue from Metal Chips:
Recovering cutting oil residue from metal chips not only helps keep the chips clean but also minimizes waste and environmental pollution. In this way, we not only optimize the cleanliness of the chips but also reduce costs related to waste disposal and protect the environment.
Reducing Chip Storage Space (up to 80%):
Utilizing our chip compaction system significantly reduces the storage space needed for chips, up to 80% compared to storing uncompressed chips. This not only reduces warehouse operating costs but also enhances management efficiency and organization in the production process.
Reducing Transportation Costs by Decreasing Chip Volume:
Reducing chip volume through compaction systems significantly decreases transportation costs. This optimization not only saves costs but also enhances the transportation process, improving the overall supply chain efficiency.
Enhancing Efficiency of Chip Transportation Operations within the Company:
The chip compaction system not only reduces time and costs in the transportation process but also enhances the efficiency of chip transportation operations within the company. This improvement not only increases productivity but also enhances flexibility and responsiveness to customer demands.
Minimizing Waste in Metal Re-melting Cases:
By minimizing waste in metal re-melting cases, we not only save raw materials but also reduce costs and enhance the sustainability of the production process.
Low Operating and Maintenance Costs:
Our chip compaction system is designed to ensure low operating and maintenance costs, optimizing efficiency and cost savings for businesses. This translates to reduced operating costs and increased profitability.
Improving 5S Operation Quality:
Using the chip compaction system not only improves product quality but also enhances operation quality following the 5S principles in the production process. By optimizing chip storage and organization processes, we ensure cleanliness, tidiness, and efficiency in the workplace, thereby increasing productivity and employee satisfaction.
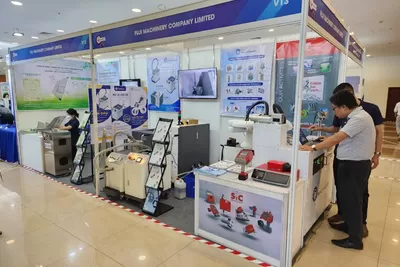
Please enter your email address
We guarantee 100% privacy - your information is never sharedWe guarantee 100% privacy - your information is never shared
Related Products
The OSD-100 oil skimmer utilizes surface skimming technology for cutting oil, efficiently removing oil sludge and impurities from the reservoir. Particularly noteworthy is its versatility, as this product does not require fixed installation, allowing flexible usage across various equipment in the manufacturing process.
The Kleanx Oil Gold Filter Machine is designed to meet the increasing demand for efficiency and environmental protection in the metal industry. With advanced technology, this machine not only removes metal shavings, sludge, and other contaminants from the cutting oil reservoir but also efficiently recycles oil and saves time.